TOMA™
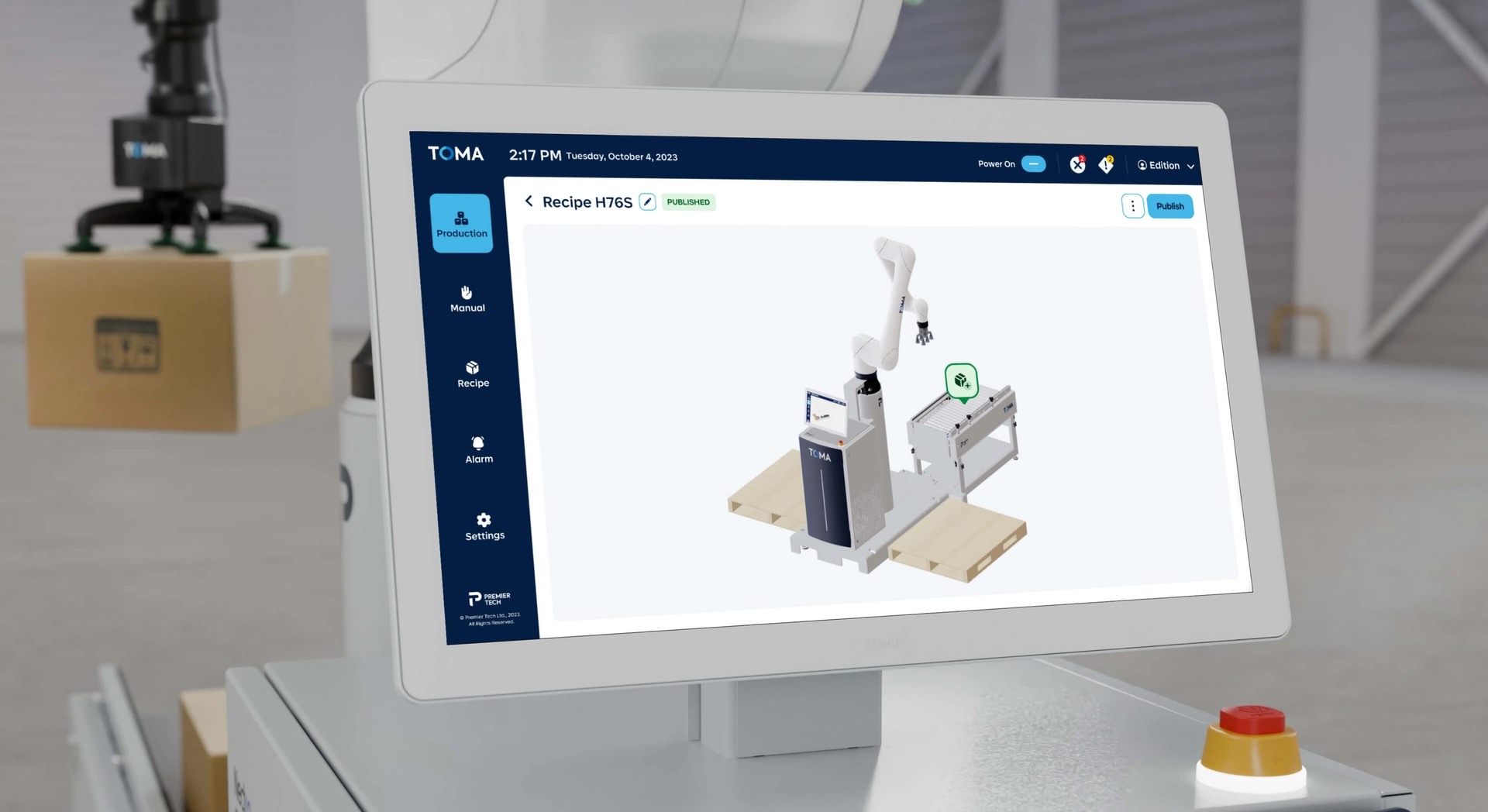
- Web
- Industrial
Context
Premier Tech has introduced a new product line designed to support packaging automation for businesses: TOMA™.
One of the flagship products in this line is an automated palletizing system featuring the market's most advanced interface, which seamlessly combines industrial strength with an intuitive user experience through collaborative robotics. With its plug-and-play integration that requires no engineering or programming, TOMA™ enables businesses of all sizes to harness the benefits of automation.
This product launch builds on over 35 years of expertise in automation and palletizing, combined with the latest advances in collaborative robotics and Premier Tech's ongoing commitment to making cutting-edge technologies accessible to a wider range of businesses, thereby driving innovation and competitiveness.
This project exemplifies a strategic collaboration between Mirego and Premier Tech, where Mirego's digital expertise seamlessly merged with PTSA's manufacturing experience to revolutionize the approach to manufacturing automation through the friendustrial™ mindset - bringing together collaborative and intuitive automation with industrial strength.
Mandate, target et objectives
Mirego was mandated to collaborate in the development of the digital platform, including the transactional website as well as the proprietary software MOVN™ that drives its configurator, simulator and the robot's user interface.
The project aimed to create an intuitive and accessible digital solution that requires no prior technical expertise, delivering user autonomy that eliminates the need for specialized technical support. This addresses the needs of two primary target markets:
Growing SMEs: Companies looking to automate specific workstations with accessible collaborative robotics solutions that require no specialized expertise
Large enterprises with variable production: Organizations that need flexible, easily reconfigurable packaging lines for seasonal products or special production runs with slower throughput (such as limited-time promotions or temporary products)
Approach
To establish the foundation for the user experience, our teams employed a methodical approach that combined qualitative research with manufacturing companies and comprehensive analysis of the industrial automation market. We aimed to understand operational realities, daily challenges, and decision-making processes surrounding the adoption of collaborative automation solutions. This comprehensive approach enabled us to clearly identify unmet needs and uncover significant innovation opportunities.
From this research emerged four major pillars that guided all of our digital product design decisions:
Workforce-centered experience
The solution must adapt to manufacturing operational realities by prioritizing autonomy and safety, while addressing labor shortage challenges and enhancing the work environment for operators.
Accessibility and simplicity at the core of the interface
Eliminating technical barriers must be an absolute priority, with an interface requiring no programming skills that enables production operators to become autonomous without relying on specialized resources.
Visualization and projection in the decision-making journey
Concrete and interactive visual representations must allow users to envision their specific context, reducing uncertainty and facilitating informed decision-making, both during configuration and solution implementation.
Digital-human balance in the overall experience
The user experience design must harmonize digital interactions with human touchpoints, adapting to the client's level of technological maturity while building trust through shared experiences and strategic guidance at decisive moments.
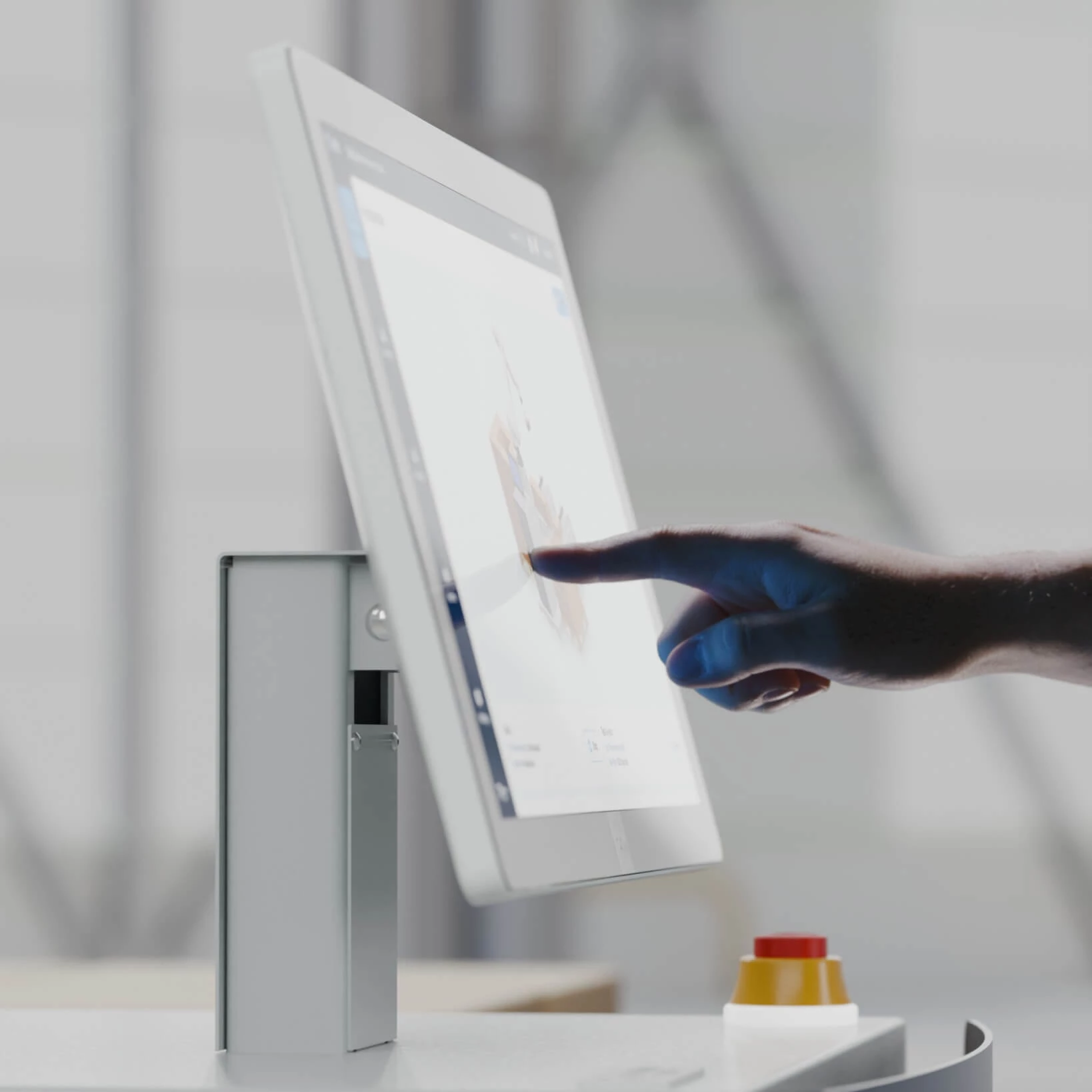
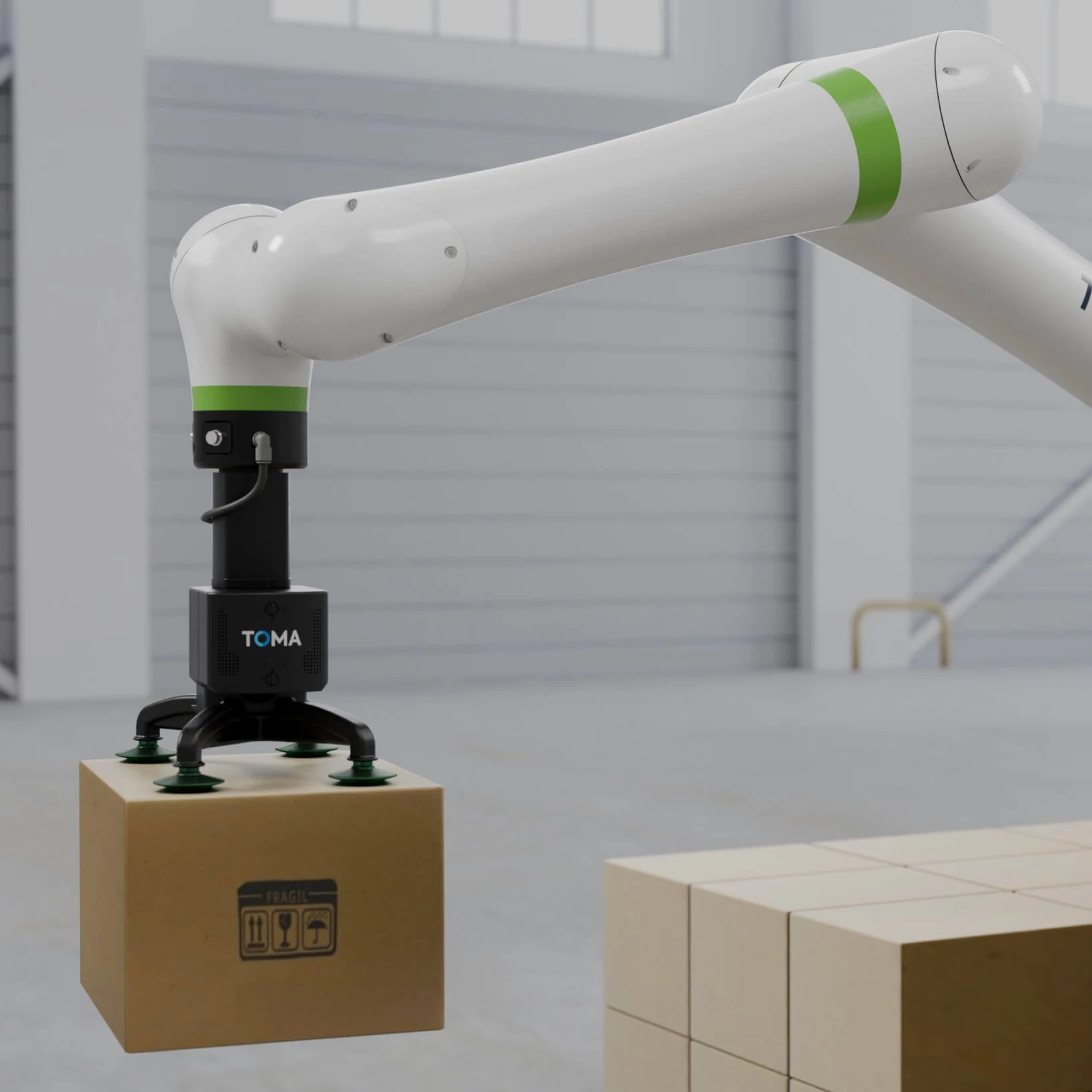
“A project like TOMA™ has enabled Mirego team members to collaborate even more closely with our Premier Tech colleagues. The strength of this partnership lies in the combination of our unique perspectives and skills, and the result is compelling: the user-friendliness of a digital platform applied to the robustness of the manufacturing industry.”
Features
MOVN™: an intuitive robotic operation software
MOVN™ is the software that powers the HMI (Human-Machine Interface) and enables factory employees to operate the robot without prior technical expertise. This solution eliminates the technical barriers typically associated with industrial robotic equipment use. Users can manage the entire operational cycle through a fluid and accessible experience.
The software offers three fundamental features, each designed to maximize operator autonomy:
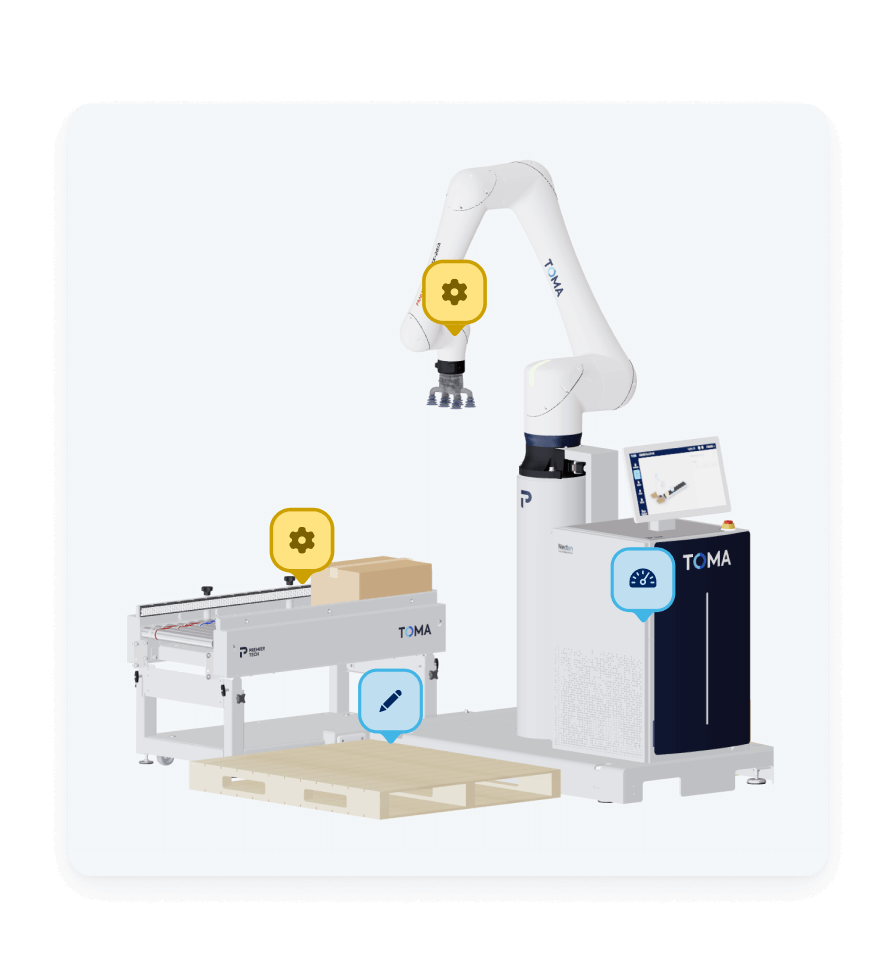
Equipment motion control
The interface allows users to configure and control all aspects of their robotic cell, including robot movements, safety parameters, and system diagnostics. The 3D equipment visualization aids spatial understanding and facilitates precise motion control.
Palletizing recipe configuration
Operators can create, modify, and save different palletizing patterns adapted to their specific needs, without writing a single line of code. The interface guides users through each step of the process with clear visualizations and contextual instructions.
Production monitoring
An intuitive dashboard displays real-time performance metrics, alerts, and important system status information. This centralized view enables operators to quickly identify and address potential issues without delay, minimizing downtime.
TOMA™: an interactive product website
The website, built on Drupal CMS, invites visitors to explore the complete TOMA™ universe.
Product features
The product pages showcase the solutions' technical capabilities and operational advantages, bringing them to life with detailed visualizations and video demonstrations. Real-world applications are highlighted through customer testimonials and case studies, building confidence in the solution's proven track record.
Configurator
Powered by React and ConfigIt for backend product management, the configurator enables users to tailor their robotic cell to their specific operational needs. The intuitive interface guides them through each available option and accessory. With seamless Salesforce integration, the system ensures smooth handling of qualified leads.
Simulator
The React-based simulator provides hands-on experience with a simplified version of the robot control interface, allowing users to test palletizing recipes before purchase. This virtual environment lets them validate the solution's fit by simulating operations that mirror their production setting.
Design System
A consistent visual interface across the TOMA™ ecosystem
In addressing this project, Mirego faced a distinctive challenge: designing a user interface specifically adapted to industrial constraints. The clean, functional design approach breaks away from the traditionally overcrowded interfaces common in manufacturing, while ensuring the industrial-grade reliability essential in this sector.
Across both platforms, the interfaces incorporate interactive 3D models for clear visualization of robotic configurations and operations. Every design element serves accessibility - from easily readable typography to contrast ratios carefully calibrated for industrial environments. The experience is enhanced through strategic animations that provide visual feedback, helping users better understand and navigate complex operations.
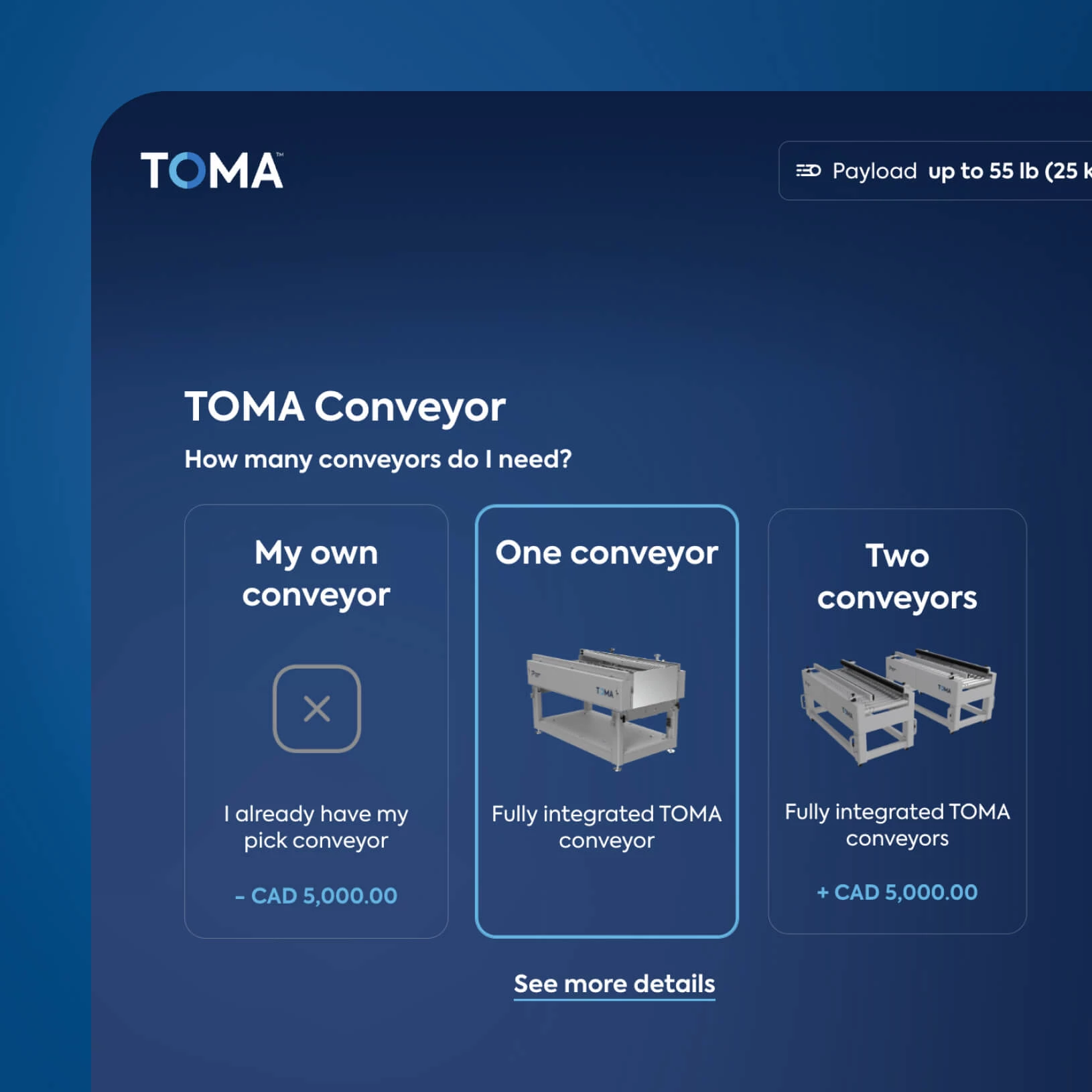
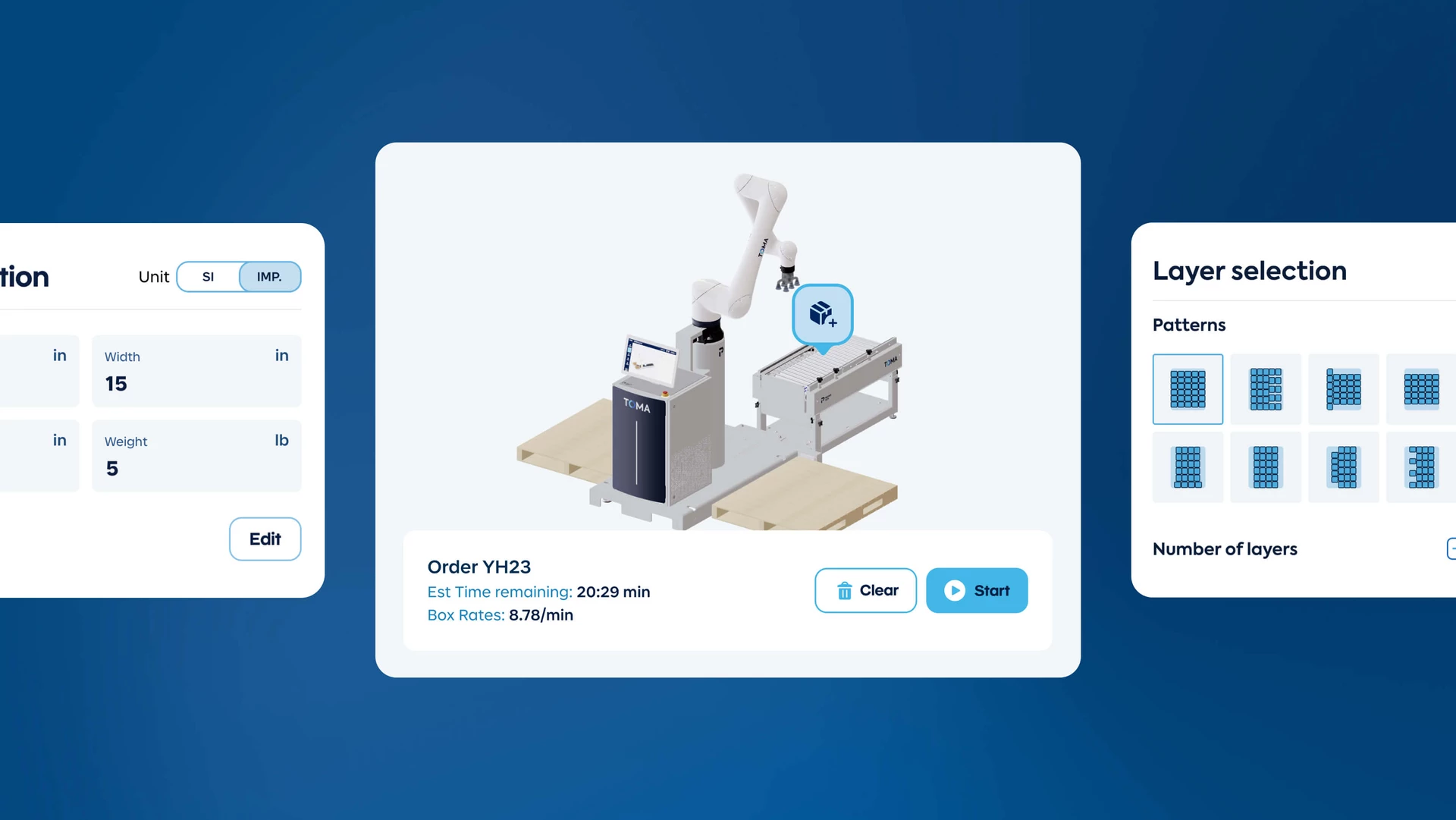
Results
Six months post-launch, the user experience has proven instrumental in making industrial automation more accessible while delivering peak performance. Here's how different businesses are transforming their operations with TOMA™:
3K
Groupe TAQ
A social enterprise supporting workers with functional limitations, Groupe TAQ implemented the solution in their food processing operations. Now handling 2,000 to 3,000 boxes daily, their team leverages the intuitive interface to run programs autonomously - no technical expertise needed. The solution also addresses workplace safety by eliminating repetitive motion injuries.
100%
This Quebec pastry maker chose TOMA™ to level the playing field with international competitors' automated processes. Set to recover their investment within a year, Boulangerie Dumas is already exploring opportunities to expand automation across their production line.